The Bedrock of Aviation—Standard Operating Procedures… Consider the Variables!
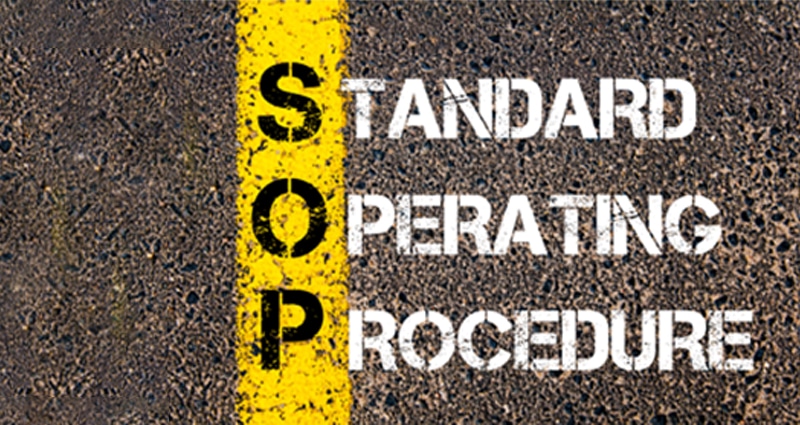
Aviation is all about standard operating procedures and their more-beloved acronym “SOP.” With the current COVID-19 pandemic and its impact on staffing levels, operators have had to make some hard decisions, whose impact may not be readily apparent. This article illuminates the risk in assuming SOPs are, in fact, standards.
Key Terms in an Important Phrase
For those who have served in the military, SOP can refer to a specific unit’s unique “standing” procedures, which may or may not be standard across a specific branch or among other units. The implication is that these standing orders are, by default, the rules to be followed.
So, outside of the military, the term, “standard” is left to interpretation when viewed by the organization that created it. The standard’s effectiveness will also be judged by the quality of instruction provided to understand and fully comprehend how the “procedure” shall be applied.
But wait, I just added a new word—“shall.” Shall is not a should but a must. So, if an organization develops and publishes an SOP, the word “standard” implies that it applies in all cases where the subject matter is affected. It is an imperative. You will accomplish this procedure based on the steps, actions or tasks that have been outlined within it.
A standard operating procedure is not a recommendation or suggestion, such that your company merely suggests you do it this way.
When used as an auxiliary verb, “shall,” according to Webster’s Online Dictionary, “denotes a requirement that is mandatory whenever the criterion for conformance with the specification requires that there be no deviation.” For good order, “must” is defined as “to be obligated,” and is a good substitute for “shall.”
On the other hand, “should” is a word that “denotes a guideline or recommendation whenever noncompliance with the specification is permissible.”
An Incomplete SOP in Action
So, let’s apply our newly defined terms to an active ramp as we happen upon an FBO apron where a recent Challenger 300 arrival is now poised to be placed in the hangar by the well-trained, well-equipped line service under the ever-watchful eye of the general manager (by the way, this is 2020!). Based on the SOP on file at this FBO, the operation should be textbook. However, in reality its nowhere close!
It begins to unravel when the supervisor, after doing the walkaround and checking the tug and towbar for the op, realizes that, based on the SOP for wing-walkers, he is short one LST from the required two to place this aircraft in the already-congested hangar. Coyly, the supervisor asks the GM to act as wing-walker and also watch the tail. The GM agrees and begins to walk over to the aircraft. Regrettably, it is at this point that I stopped the operation to ask a few questions of the supervisor.
“I see you checked the tug and it is appropriate for this aircraft and ramp in the current conditions. I see you checked the tow bar and did a visual inspection of the nose gear to ensure it was secure and the bypass pin was removed. I see you did a walkaround of the aircraft and checked the hangar doors and parking area to ensure the aircraft would fit.”
So far, so good.
“Do you have an SOP for these types of movements? As you are inviting a new member, the general manager, to join your team, have you asked him if he is aware of the SOP and been trained or briefed on it?”
The answer, of course, was no. The supervisor had assumed that since the GM was management, he would be aware of the rules. Unfortunately, assumptions very often lead to increased risk!
Next, I asked if the supervisor discussed the tow plan with the other LST and the new member (the GM), and again the answer was no. The purpose of the pre-tow discussion is so that everyone on the ”team” is aware of the complete task, the position they will take, the check of required PPE (vest, whistle), the path of the aircraft and the identification of hazards (other aircraft already in the hangar, the hangar wall and door height, etc.), so that the most appropriate (most experienced or aware) wing-walker can watch the hazard areas and ensure that the tug operator is keenly aware of distances and closure rate.
I then turned to our newest member of the team, and learned that he was aware of the SOP but wasn’t wearing the required vest and did not have the required whistle (for emergency stop, as it is better than a visual hand signal). So, while there was some awareness, there wasn’t a sense that this was a standard! This added a lack of detailed knowledge to the growing list of elements that increased the risk of the operation.
As the scenario continued, we equipped the GM with the required safety vest and whistle, went over the SOP as written, and agreed that we needed to add that the supervisor may stop the movement at any time to allow the wing-walkers to get in proper position for maximum visibility of the hazard area.
Due to the team’s lack of experience working together, I stressed that the tow didn’t have to be continuous, but rather had to allow for the wing-walkers/tail-walkers to get into position to ensure they had the best view of any obstacles that might become a source of damage while also maintaining a continuous line of sight with the tug operator.
Lessons Learned
So, what’s the lesson here? While the SOP as written seemed to address the activity as standard, it did not consider variables, such as inexperience or the time it takes a wing-walker to move to a proper position to visualize the hazards and provide clear guidance.
SOPs are intended to be followed exactly as documented, consistently, every time. That means that they should be developed thoughtfully and completely based on the type and complexity of operation and trained to ALL staff that may be required or asked to support the operation, taking into consideration the vagaries of individual competency. The procedures should then be checked routinely to ensure they remain accurate for the op.
Yes, it’s a standard operating procedure, but now it anticipates variables that are ever-present in aviation!
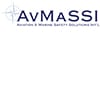
AvMaSSI provides safety, security and operational integrity evaluations, consulting and auditing to airlines, airports, charter and corporate operators, OEMs, marine operators, seaports, governments, international agencies and financial institutions the world over. AvMaSSI provides IS-BAO and IS-BAH preparation and audit services and supports Global Aerospace and its SM4 and Vista Elite Programs with focused safety/SMS, security, regulatory compliance and IS-BAO auditing services. AvMaSSI is a proud member of the Global Aerospace SM4 partnership program.
http://www.Avmassi.com
© 2024 Aviation & Marine Safety Solutions International. All Rights Reserved.
Next ArticleRelated Posts
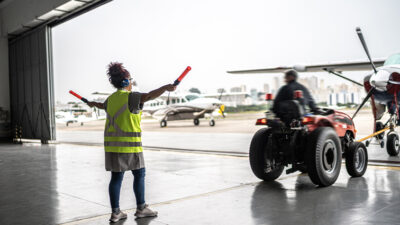
The Effects of a Learning Mindset on Safety Culture
As aviation departments strive to enhance their safety performance, a critical yet often overlooked element is the need to foster a learning-culture mindset. This mindset shift can unlock invaluable opportunities for continuous improvement, employee engagement and creating a resilient safety environment. From a behavioral management perspective, as your company’s learning culture goes, so goes the ongoing success of your SMS.
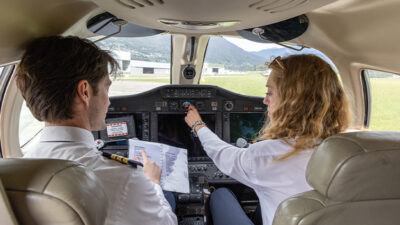
Safety in Numbers: Trends in Aviation Accidents and Incidents
Every accident is preventable; the problem is that we don’t know how to prevent it until after the accident happens. However, what we can do as an industry is honor the anguish of each event by sharing the information, the mistakes and the outcomes to improve safety for everyone.