OSHA is Coming to General Aviation
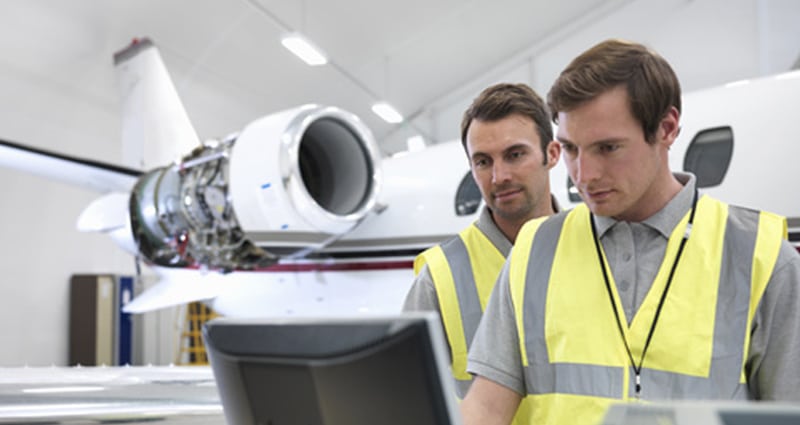
General aviation operators have always been subject to OSHA regulations, but have historically been under the radar of regulators, who have bigger fish to fry. Also, in some respects it has been unclear to regulators and operators alike whether OSHA or the FAA have jurisdiction in certain aspects of aircraft operation. Recent news releases, however, report that our community will be getting greater scrutiny in the near future.
The changes stem from a Memorandum of Understanding between OSHA, the FAA, and the U.S. Department of Labor, reached in August 2000. By that agreement the FAA was to issue a new policy statement “setting forth the circumstances under which the regulatory requirements of OSHA will apply to the working conditions of employees on aircraft in operation (other than flight deck crew.)”
Only 13 years later we have an answer.
On the Aircraft
A coming change affects cabin crewmembers on aircraft in operation. Note that this specifically excludes pilots, but includes others who have assigned duties in the cabin, whether they are called flight attendants, cabin attendants, technicians, observers, or any other name. It also includes those who may occupy the jump seat during takeoff or landing if they fulfill any duties in the cabin. An aircraft is “in operation” from the time it is first boarded by a crewmember, preparatory to flight, until the last crewmember leaves the aircraft after completion of flight, including stops on the ground during which at least one crewmember remains on the aircraft even if the engines are shut down.
By the new policy, the FAA has agreed that OSHA regulations apply to cabin crew members in three specific areas:
- hearing conservation inside the aircraft;
- bloodborne pathogens, and
- hazard communication
Primarily, the operator’s responsibility falls in training to recognize these hazards and, where necessary, to mitigate risk.
For its part, OSHA anticipates that it can respond to and investigate complaints without a need to inspect aircraft in operation. Enforcement will rely on OSHA’s regulations on record keeping and access to employee exposure and medical records. Where states and localities have their own regulations for occupational health and safety, federal OSHA will ensure that aircraft operators are not subject to multiple sets of rules.
In the Hangar
In a broader application of the hazard communication standard, a new OSHA regulation requires training of all flight department personnel by Dec. 1, 2013. Additionally, new labeling and a standard format for safety data sheets (SDS), formerly called material safety data sheets (MSDS), is required for all hazardous chemicals stored in the workplace. A large multiaircraft flight department that performs its own aircraft maintenance might easily have 150 potentially hazardous substances in the hangar, according to one experienced aviation maintenance manager.
Labeling on hazardous material containers must contain the name, address, and phone number of the manufacturer or distributor. Training must cover recognition of “Danger” or “Warning” signs on hazardous materials, reference to and use of safety data sheets, and information on minimizing the effects of exposure to a hazardous chemical. Fuller information about this requirement can be obtained at https://www.osha.gov/dsg/hazcom/index.html.
Two years ago, Andreas Bentz of Chantilly Air, Inc. gave an excellent presentation at the NBAA annual meeting that covered OSHA requirements for business aviation (prior to these changes). Check out his presentation at http://www.nbaa.org/events/amc/2011/news/presentations/1010-Mon/NBAA2011-1010-1500-OSHA-Business-Aviation.pdf.
If you think this doesn’t affect you, you’re wrong. Aviation managers often tell me that their responsibilities regarding OSHA regulations are covered by the FBO with whom they rent hangar and office space. While it is fair to seek assistance and cooperation from the building owner, it must be understood that the employer is responsible for the safety of employees in your work place, not any third party. The employer has both a moral and a legal obligation to protect the safety and welfare of its employees. That responsibility falls to the Aviation Manager.
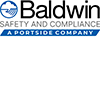
Customized Safety Management programs developed by experienced and credentialed safety professionals include training, manual management and SMS implementation/software. Based on ICAO and other international standards and regulations, Baldwin’s programs support Business Aviation, Charter, FBO, Airport, Medical Transport and Regional Airlines by providing advanced software, an outstanding customer experience and our Commitment to Excellence.
http://www.baldwinsms.com/
© 2025 Baldwin Safety & Compliance. All Rights Reserved.
Next ArticleRelated Posts
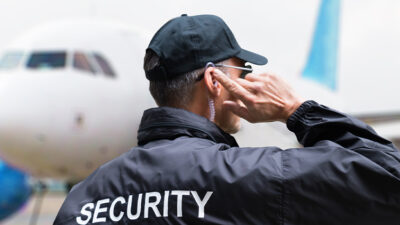
Emerging Security Threats in Business Aviation: Activism and Down-Route Risks
Security incidents affecting business aviation do not need to involve violence to have an operational impact. A protest delaying crew movements, blocking access to a hangar or resulting in an unauthorized photograph of a sensitive client can all trigger reputational, financial or compliance concerns for operators.
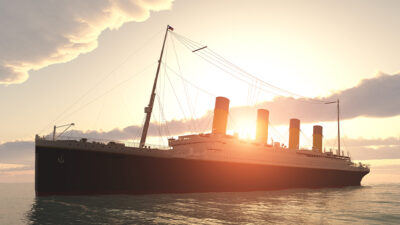
Little Things Matter: The Lost Key of the Titanic
Ultimately, the story of the Titanic’s lost key is a call to action for aviation professionals. It underscores the need for unwavering attention to detail, robust systems to catch human error and a culture that prioritizes safety over haste.